The term ‘unpiggable,’ while having no universally accepted definition, best describes pipelines that are difficult to inspect internally with conventional in-line tools such as smart pigs.
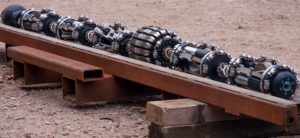
Diameters
- Multi diameter
- Small diameter
- Thick or thin walled pipe
- Repair section in different size
- Over or under sized valves
- Fabricated (mitred) bends
Bends and connections
- Back to back bends
- Unbarred tees
- Y connection
- Short radius or mitred bends
- Dead legs, cross overs, and laterals
Flow and access
- Difficulties of access (offshore platforms, subsea)
- Low or no flow
- Cleanliness of the pipe
- Pipeline without pig launcher or receiver
Older pipelines
- Cased road or river crossings
- Bore restrictions
- Steep and vertical sections
- Installations such as plug valves, dead ends, off-takes, etc.
In-line inspection (ILI), such as pigging, is an important process to maintain the integrity of a pipeline. ILI tools are used to survey the pipeline and assess failure risks such as corrosion, blockages or leaks. These inspections can also help uncover important information about the pipeline and fill ‘gaps’ of knowledge.
The impacts of pipelines that are not inspected can lead to a number of problematic scenarios including pipeline failure. With proper and scheduled maintenance of pipelines you decrease the chances of the pipeline failing.
Key technology advantages
- High reduction passing
- Tight bend passing
- Multi-diameter capacity
- Extremely high driving force enables vertical climb
- Self-adapting tractor drive unit in one body
- Intelligent and redundant
- on-board mission control
- Single entry to the pipeline
- Capable of safely negotiating 1.5D bends
- Bi-directional operation Autonomic (only batteries) or tethered (external cable with communication) operation possible
- Reliable in various media (water, gas, crude oil and dual-phase products)
- Sensor carriers (Shallow Internal Corrosion, UT, EMAT, etc.)